DeepDP
Deep learning-based Defect Prediction
Deep learning-based Defect Prediction (DeepDP) is a deep learning model-based solution for predicting product defects in advance using process setting values and environmental factor data.
DeepDP receives as input the set values of process variables and current data from various sensors such as temperature, pressure, current, and speed installed in the process, and predicts the product defect or the value of indicators such as defect rate in the process. It also provides identification of process variables and process sensors and time intervals that are potential causes of current failures. It is also possible to extend the function to classify multiple defect classes or types to cope with complex processes or different types of failures.
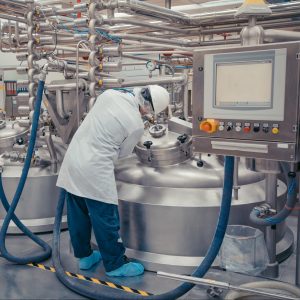
Enables Preemptive Quality Control and Early Defect Prediction in Manufacturing Process
Factory production quality is a key competitive factor in manufacturing, but it is often overlooked in process control because it is difficult to measure or evaluate compared to output and other visible indicators. Quality measurement is often performed after the completion of process, so it is difficult to evaluate the quality level of a product in real time in the middle of process. Usually, in the case of quality measurement in process, sampling measurement is used, and thus there is a problem that is not highly correlated with the final quality of a product. The introduction of an in-process quality or defect prediction system enables preemptive quality control and early defect prediction in manufacturing process.
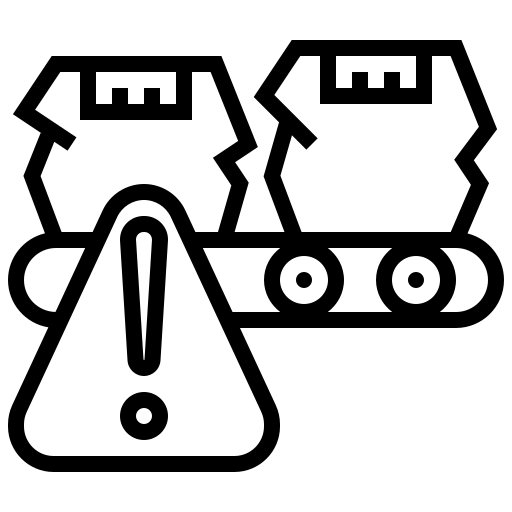
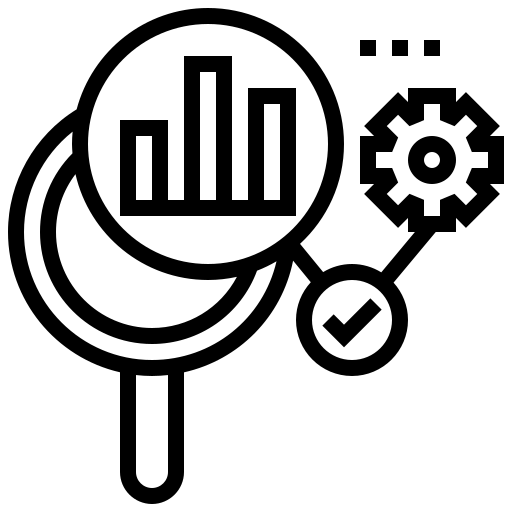
Provides Fast, Proactive Prediction for Failures
In manufacturing process, there are basically various failure factors such as setting errors, human variables and environmental factors. Therefore, process defects are likely to occur at any time, and thus real-time countermeasures must be taken at the point when actual defect detection increases. For the occurrence of high frequency defects, it is necessary to fundamentally solve the problem by identifying the causal process, environmental variables, and data characteristics. This can be clarified to some extent by figuring out which variable or input data for which time interval is the potential cause of defect. This information can also be used to build automatic feedback sequences to eliminate defect causing factors.
Contributes to Productivity Improvement by Reducing the Defect Rate
DeepDP contributes to reducing the defect rate by enabling preemptive countermeasures against possible product defects in manufacturing process. By utilizing the information obtained through process defect prediction, field workers can improve their process management skills. By identifying the exact cause of process defects, it is possible to fundamentally improve equipment and process problems. Eventually, it contributes to productivity improvement by reducing the defect rate.
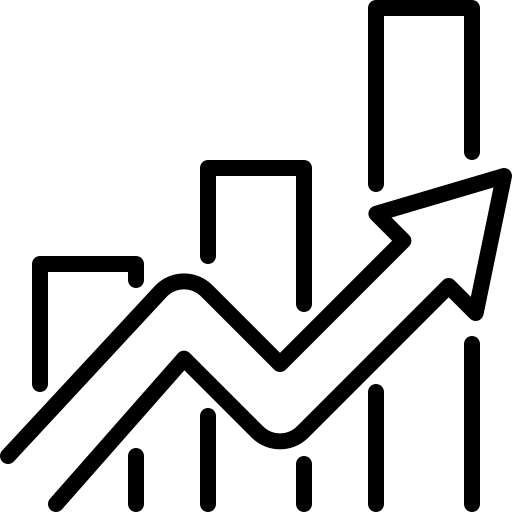
Use Case – Injection Molding Process
Injection molding, in which liquid material is injected into a fixed shape frame and then cooled to make the product, controls several factors such as temperature, pressure, and time under process conditions. If the operator incorrectly sets the process conditions, a defect will occur. These factors are also closely related to the surrounding environment, and as environmental factors change, the defect rate increases even under the same process conditions. Therefore, a system is needed to predict and warn of possible product defects in real time, depending on the process conditions and environmental factors of the current molding cycle.
We build a product defect determination dataset that matches temperature, pressure, speed, and time sensor data of injection molding machines with ambient condition sensor data and learn a defect prediction deep learning model to predict defects from real-time sensor data.
Real-time defect response measures reduced the defect rate by 3%. We were also able to derive a process condition optimization plan based on changes in environmental factors.